Tundra offers platforms optimized with performance properties for specific applications.
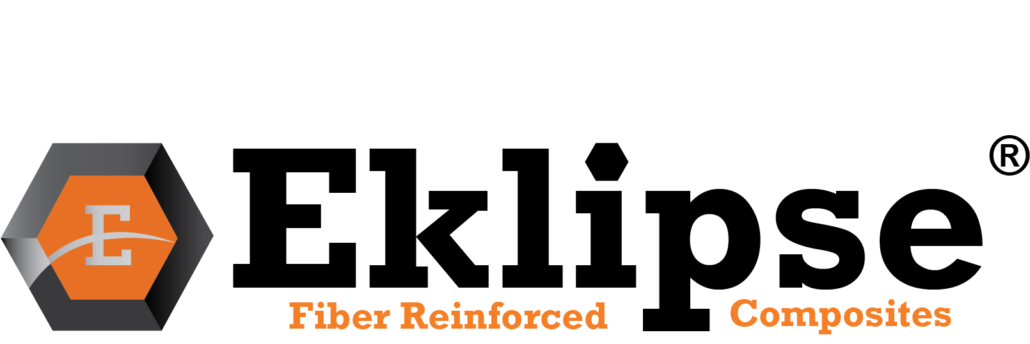
Deliver game-changing performance and affordability to a variety of products.
Eklipse® composites contain a fiber with an aspect ratio greater than 3:1 in a thermoplastic or thermoset.
The Eklipse® platform allows you to create products that perform better in applications that require: structural integrity, decreased coefficient of thermal expansion, or increased heat distortion temperature.
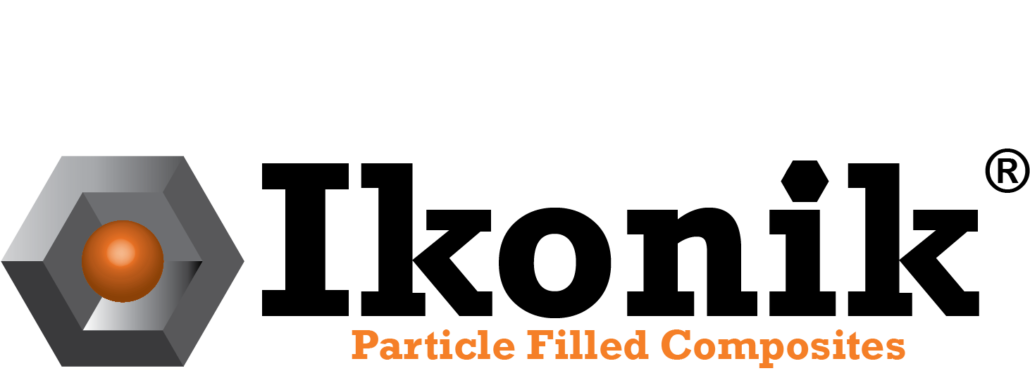
Provide cost-effective non-toxic alternatives to other high- or low-density materials.
Ikonik® composites incorporates particles to serve a specific function in a thermoplastic, thermoset, hot melt or rubber.
The Ikonik® platform allows you to create composite products that are heavier, lighter, more easily processed, polymer extenders, or magnetic.
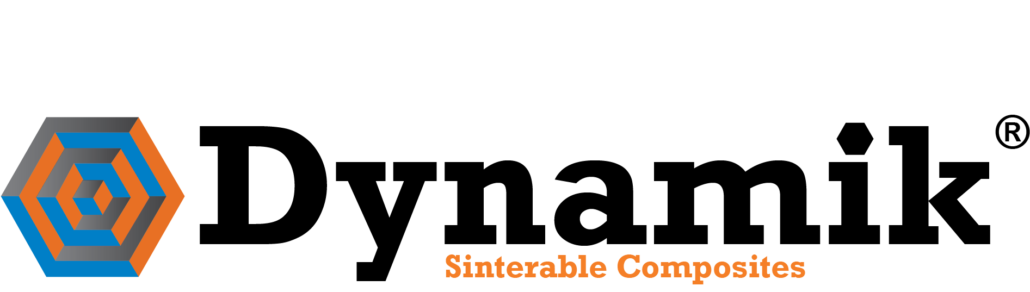
Deliver processable materials optimized for injection molding and 3D printing.
Dynamik® composites are highly packed with metal or ceramic particles that can be processed via metal injection molding (MIM), ceramic injection molding (CIM), and additive manufacturing (AM).
The Dynamik® platform sets a new standard for metals fabrication efficiency, adding speed and economy through the unique application of plastics forming technology. The end result is metal composites with tensile, flexural, hardness, smoothness and other properties that meet MPIF Standards.
Tundra can assist you at any stage of materials innovation — from idea and development through technology transfer and production.